Which scale prevention strategy is right for your pharmaceutical water system?
Reverse osmosis (RO) technology is now ubiquitous in water purification. While older system designs sometimes relied on distillation as a main purification strategy, RO has become the standard workhorse even for producing water for injection (WFI) under most pharmacopeia. Need a refresher on how purified water systems work? Check out our overview article here.
RO is a fantastic technology when properly applied. It is quite sensitive, though, and it’s important to make sure that the water your RO membranes are purifying is not going to damage them or foul (plug) them. RO membranes are quite easily plugged by scale, which is caused by hardness exceeding its rather low saturation limits on the “dirty” side of the RO membrane. This is why RO pre-treatment usually includes a step either to remove hardness or to increase its saturation limit.
After reading this article, you should have a relatively clear understanding of which technology will be best for your circumstances. We’ll compare three technologies: softeners, anti-scalant chemical dosing and electrolytic scale removal (ESR).
Factors Considered
For each technology, we’ve evaluated capital cost, direct operating expenses, reliability, negative downstream impacts, maintenance and operating requirements and footprint. Depending on your priorities, each of these factors will be more or less important to you. For this reason, we strongly recommend completing a thorough analysis of your requirements prior to selecting any treatment technology.
We provide the results of our comparison in the summary table below and explain our rationale around all criteria except footprint in the subsequent sections.
Summary
|
Softening |
Antiscalant |
ESR |
Capital Cost |
$$ |
$ |
$$$$ |
Annual Operating Cost |
$$$$ |
$$$ |
$ |
Reliability |
|
|
|
Negative downstream Impacts |
XX |
XXXX |
X |
O&M Requirements |
+++ |
++ |
+ |
Footprint at 5 US GPM |
6’x2’ |
3’x3’ |
5’x5’2 |
Footprint at 80 US GPM |
8’x12’ |
3’x3’ |
6’x11.5’ |
High-level comparison of softening vs. antiscalant vs. ESR
1 We’ve assumed that antiscalant use will result in more frequent membrane replacement. For OpEx estimates excluding the membrane replacement costs refer to the detailed Operating Expense section.
2 Footprint for ESR is our best conservative guess based on available data sheets, which are for complete purified water and WFI systems. Actual footprint may be smaller.
Reliability
All three options presented here are relatively reliable. When evaluating reliability we’ve considered both the reliability of the equipment itself as well as its sensitivity to changing feed water quality.
Reliability of Softeners
Softeners are a very old, tried and tested technology. If properly maintained, they typically work very well and rarely break down. Furthermore, they can be adjusted to reliably treat the “worst case” of feed water quality without causing negative downstream effects.
They are prone to mechanical failure, though, especially when maintenance tasks aren’t performed frequently or diligently enough. For example, the brine system must be cleaned on a regular basis to prevent clogs and other malfunctions that would result in the softener passing hard water to the RO system. They often include complex multi-port valves or valve nests that have a large number of seals and moving parts that can fail. Even with these possible failure points, diligent maintenance, which is very common in the pharmaceutical industry, typically keeps softeners running very reliably.
Adding to the reliability factor of softeners is the fact that they effectively remove other cations such as iron, which can be a problem for reverse osmosis machines protected with antiscalant and ESR.
Reliability of Antiscalant
Antiscalant chemistry works very well within specified water quality parameters. With that said, antiscalant dosing systems do rely on relatively stable feed water quality, especially pH and hardness. Contrary to softeners, incorrect dosage due to variable feed water quality may lead to premature fouling of the reverse osmosis membranes.
Like any chemical dosing system, regular maintenance of the dosing pump(s), tubing and valves is necessary to prevent clogs and other malfunctions.
Reliability of ESR
Electrolytic scale reduction is by far the option with the fewest moving parts. For this reason, it can be reasonably expected that an ESR system that has been correctly sized for the feed water quality and flow will perform well as long as recommended maintenance is performed.
Unfortunately our team does not have direct experience or customer data on ESR technology reliability. We’ve used filmed customer testimonials, feedback from clients using ESR in cooling tower applications and a technical analysis of the technology as our basis for expected reliability.
From this experience it is our understanding that ESR is very reliable when operated within relatively narrow design parameters. If water quality including pH and hardness tend to swing significantly in the feed water, we expect that premature RO membrane fouling may result. With that said, ESR sized for the worst case scenario would likely be the most reliable solution for pre-RO scale reduction available today.
Negative Downstream Impacts
While pretreatment technologies obviously exist to protect downstream purification equipment, all three technologies significantly change the water chemistry and so it’s important to be aware of the potentially negative effects they have on the RO system and the water quality it will produce.
Negative Downstream Impacts of Softeners
Softeners replace most divalent and trivalent cations in the feed water with monovalent sodium ions. While this is relatively benign, it’s important because reverse osmosis membranes have a much easier time rejecting divalent and trivalent ions than they do rejecting sodium. In short, this means that one can expect softening to increase the conductivity of reverse osmosis permeate in proportion to the non-sodium cation loading of the feed water.
In most cases, the amount of sodium added to the feed water is not significant enough to cause a real process issue. When purifying heavily charged (high conductivity) water, however, it may be worth exploring other options if the first pass RO conductivity is a limiting design factor.
Negative Downstream Impacts of Antiscalant
While antiscalant dosing is one of the most popular approaches to scale prevention in large (>30 US GPM) RO system operation, it’s also the method we’ve seen most often lead to short membrane life. A review of the scientific literature reveals that antiscalant dosing must be very precise to be highly beneficial. Underdosing antiscalant can obviously lead to membranes fouling with scale (hardness or metal deposits on the membrane) while overdosing can lead to the antiscalant itself depositing onto the membrane. It has also been observed that the use of polymer-based antiscalants significantly increases biological fouling.
In short, while antiscalants are the least costly solution, they are the one that typically causes the most downstream headaches and costs.
Negative Downstream Impacts of ESR
Other than the obvious negative impact of an incorrectly sized ESR system – that of membrane scaling due to significant hardness leakage – we couldn’t identify any other suspicious negative downstream effects. It’s worth noting that ESR is actually actively removing contaminants from the water stream, making the RO’s job easier beyond just preventing scale buildup on the membranes.
One small detail we’ve noted is that ESR manufacturer BioPureMax indicates that some free chlorine is generated in very small amounts by ESR systems (source). We don’t see this as a significant concern as we would expect the ESR step to be followed by some sort of dechlorination step across all systems where it is installed.
Furthermore, manufacturers of ESR technologies claim that the technology removes hardness to effectively prevent scaling on RO membranes. We would be cautious about using ESR when designing high-recovery RO systems that concentrate the feed stream more than the 4x concentration seen in systems operating at a relatively standard 75% recovery.
Operation & Maintenance Requirements
In this section we consider how much operator intervention is required to adequately operate and maintain each of the three scale prevention options. We cover these requirements separately from the operating expenses tied to each option because some clients find certain requirements to be particularly onerous irrespective of their cost implications.
O&M Requirements for Softeners
The most obvious operating requirement for softener systems is that of loading salt into the softener’s brine tank. In most pharmaceutical water purification systems, this is a manual operation rather than a machine-assisted or automated process like in plants with large central brine systems.
Beyond the requirement to refill the brine tank, usually on a weekly basis, softeners should be monitored for hardness leakage, preferably with online hardness analyzers. Other maintenance tasks such as brine tank and brine valve cleaning, verifying the operation of regeneration cycles and testing resin capacity need only be done annually or semi-annually.
Dans l'ensemble, les adoucisseurs nécessitent le plus d'interventions de la part de l'opérateur et certainement les travaux les plus lourds (au sens propre) des trois options de prévention de l'entartrage. Cela dit, ils restent très faciles à gérer pour la plupart des usines pharmaceutiques.
O&M Requirements for Antiscalant Systems
Antiscalant dosing systems require regular monitoring of inlet hardness and adjustments at the dosing pump when hardness levels fluctuate. Otherwise, these systems are relatively low maintenance, requiring a quick visual inspection to make sure there are no clogs or leaks and that the antiscalant is flowing as expected.
Some operators prefer to deal with as few hazardous chemicals as possible. In these cases, antiscalant can be an option to avoid, despite the relatively limited operator intervention required to replace buckets or barrels periodically. The chemicals are also relatively easy to handle.
O&M Requirements for ESR
ESR systems operating within their specified design parameters are very low maintenance. Typically, they are self-cleaning, reversing current and automatically flushing accumulated precipitate on a daily basis. These systems may require a simple cleaning with a pressure washer about once a year to avoid performance loss. What’s more, one can monitor their effectiveness and the need for a cleaning by monitoring their power draw. They draw more power as the resistance between the anode and cathode decreases with scale buildup.
Cost Comparison
All OpEx calculations are based on 24/7/365 operation and 10 grains per gallon of hardness.
CAPEX
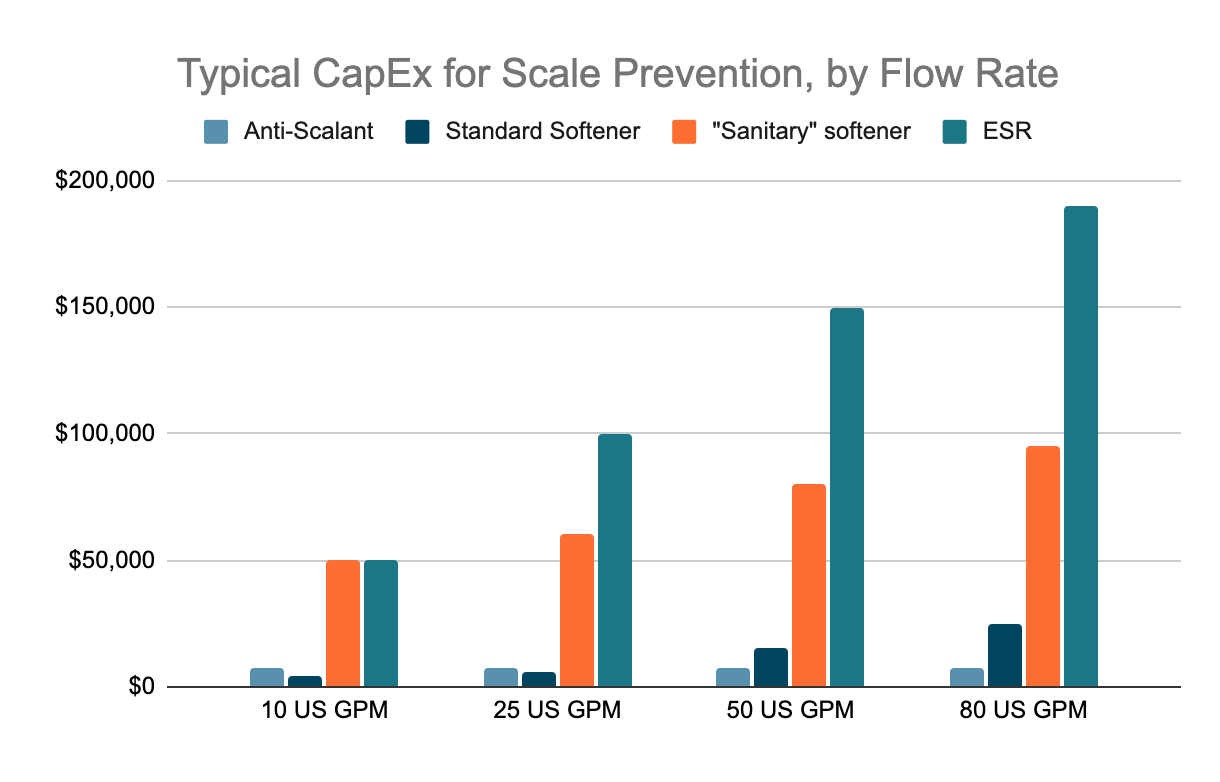
OPEX
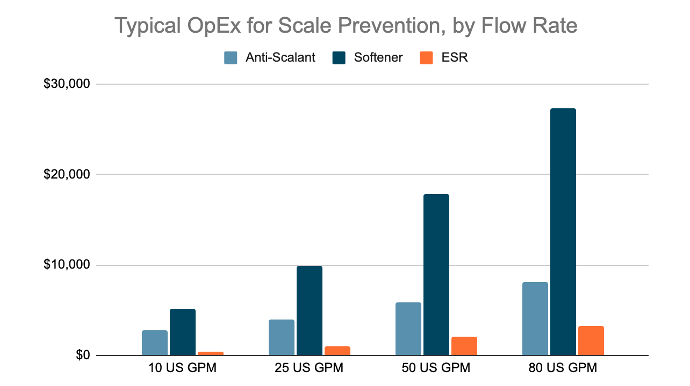
Softener OpEx based on two maintenance visits at $1 000 each and a cost of $6 per 18.1kg (39.8lbs) bag of salt, dosage of 10 lbs of salt per cubic foot of resin and capacity of 25 000 grains per cubic foot of resin.
Antiscalant OpEx based on dosage of 4.5 mg/L of SUEZ’s Hypersperse MDC700 at a price of $8.57/kg and $2 000 of annual pump maintenance cost in parts and labour.
ESR OpEx based on power costs of $0.09 / kWh.
For more information on the cost of pharmaceutical purified water systems, read our article here.
Conclusion
Choosing the best scale prevention solution for your purified water system is not a simple decision. There is simply no “best” technology, although there is almost always a “best choice” for a given application when a thorough needs assessment including technical, economic, environmental and human factors has been completed.
What are your best practices in scale prevention for pharmaceutical water systems? Join the conversation by leaving a comment below. We’d love to hear your thoughts!